Summary:
Essential Conveyor System Parts for Efficient Material Handling
What Are Conveyor System Parts?
Essential Conveyor System Parts for Smooth Operations
How Conveyor System Parts Improve Efficiency and Productivity?
Selecting the Right Conveyor System Parts for Your Needs
Maintenance and Care of Conveyor System Parts for Longevity
In any modern material handling system, a conveyor system is an indispensable component. Whether in manufacturing, logistics, or warehouse management, conveyors play a crucial role. To ensure materials move smoothly from one location to another, each conveyor system part has a specific function. Understanding how these parts work together not only enhances overall system efficiency but also helps businesses save on costs and reduce downtime.
What Are Conveyor System Parts?
Conveyor system parts refer to all the components that make up a complete conveyor system, from the conveyor belt itself to the supporting structure, power source, and control systems. Each part plays a critical role in the smooth operation of the system. Major conveyor system parts include: conveyor belts, drive units, rollers, tensioners, and motors. These components work in harmony to ensure that materials are moved efficiently and continuously through production lines or warehouses.
For example, the conveyor belt is the primary element that carries materials, using friction to move items along the conveyor path. The drive unit is responsible for powering the conveyor belt, ensuring continuous movement. Rollers and tensioners help maintain proper tension on the belt, ensuring it doesn’t become too loose or too tight, which could affect efficiency.
The Role of Conveyor System Parts in Material Handling
Conveyor system parts play an essential role in material handling. Each part supports the smooth transport of materials, allowing them to flow seamlessly through the production or warehouse process to improve efficiency. For example, the drive unit transfers power from the motor to the conveyor belt, ensuring that there is enough force to move the items. Rollers help support the conveyor belt, reduce friction, and ensure that the belt moves smoothly.
Additionally, some components, like tensioners, adjust the tension of the belt, ensuring materials don’t get stuck or go off-track. This is crucial for efficient material handling. Control systems also play a significant role, offering automated control that ensures precision and stability, reducing the need for manual intervention.
Key Benefits of Understanding Conveyor System Parts
Understanding conveyor system parts and their functions not only helps optimize the efficiency of an existing system but also allows for quick problem diagnosis when issues arise. By gaining a deeper understanding of how each component works, businesses can better maintain and care for their systems, minimizing production delays due to component failures.
Additionally, this knowledge can aid in making informed decisions when purchasing new equipment, ensuring that the right parts are selected to suit specific needs. Whether it’s for improving material handling efficiency, reducing energy consumption, or enhancing the reliability of production lines, understanding how conveyor system parts work together is crucial to improving productivity and operational efficiency.
Essential Conveyor System Parts for Smooth Operations
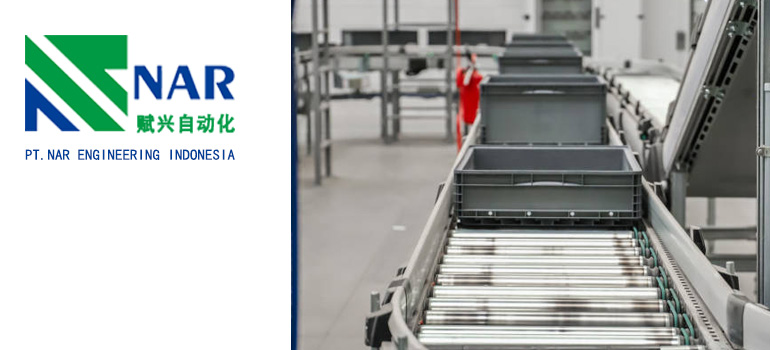
A well-functioning conveyor system relies on a variety of key components working together seamlessly. Each conveyor system part has a specific function that contributes to the system’s overall efficiency, reliability, and safety. When these parts are properly selected, installed, and maintained, the system operates smoothly, ensuring that materials are moved efficiently and safely. Below are the essential conveyor system parts that are crucial for smooth operations:
Conveyor Belts: The Backbone of Material Handling
Peralatan conveyor belt is the most critical part of the system, serving as the primary medium for transporting materials. It is typically made from materials such as rubber, PVC, or metal, depending on the type of material being moved and the environment in which the conveyor is operating.
Function: The belt provides the surface on which materials are placed and moved along the conveyor path. It uses friction to transport goods from one end of the conveyor to the other, which makes it the backbone of the system.
Importance: The durability and strength of the conveyor belt directly affect the overall performance of the conveyor system. Choosing the right belt material for specific applications (e.g., heat-resistant, oil-resistant, or food-grade belts) is essential to ensure smooth operation.
Maintenance Tip: Regular inspections for wear and tear, as well as proper tensioning, can prevent issues like belt slippage, misalignment, or breakage, ensuring the system runs smoothly.
Rollers and Idlers: Ensuring Smooth Movement
Rollers and idlers play a key role in supporting the conveyor belt and ensuring smooth movement of materials. These parts help distribute the weight of the load and reduce friction, which contributes to the efficiency of the system.
Function: Rollers are cylindrical parts that are placed beneath the conveyor belt to support its weight and enable its movement. Idlers are similar to rollers but serve more to maintain tension and prevent the belt from sagging.
Importance: Properly functioning rollers and idlers reduce friction and prevent excessive wear on the conveyor belt. They help the system run more efficiently by ensuring that the belt moves smoothly and that materials are transported with minimal resistance.
Maintenance Tip: Regular cleaning and lubrication of rollers and idlers, along with timely replacement of damaged components, can prevent breakdowns and increase the lifespan of the conveyor system.
Motors and Drives: Powering Conveyor Systems
Peralatan motor and drive unit are essential for powering the conveyor system and enabling the movement of materials. These components provide the energy required to turn the rollers and move the conveyor belt.
Function: The motor generates power and transmits it through the drive unit (such as a gearbox or pulley system) to the conveyor belt. This drives the belt’s movement, allowing the system to transport materials over long distances or across different levels in a facility.
Importance: The motor and drive unit are integral to the system’s reliability and speed. The power and speed of the motor must be appropriately matched to the system’s capacity to ensure smooth and consistent operation.
Maintenance Tip: Regularly check the motor for signs of overheating or wear. Keeping the motor and drive unit well-maintained through lubrication and monitoring will reduce downtime and extend the life of the system.
Tensioners: Maintaining Optimal Belt Tension
Tensioners are an important component for ensuring the correct tension on the conveyor belt. These parts help to keep the belt taut, preventing it from slipping or sagging, which can lead to inefficient operations and potential damage to the system.
Function: Tensioners adjust the tension of the conveyor belt to ensure that it stays tight enough to function properly without being too loose or too tight. This balance ensures smooth and consistent movement of materials along the conveyor.
Importance: Correct belt tension is crucial for maintaining smooth operations. If the belt is too loose, it can slip or derail, while if it’s too tight, it can cause excessive wear on the motor, drive unit, and other components.
Maintenance Tip: Regularly inspect the tensioner mechanism for any signs of wear or misalignment, and adjust the tension as necessary to maintain optimal performance.
Control Systems: Ensuring Precision and Efficiency
Control systems are vital for automating and managing the operation of the conveyor system. These systems include sensors, programmable logic controllers (PLCs), and software that ensure the system operates with high precision, adapting to varying speeds and loads.
Function: The control system regulates the speed, direction, and operation of the conveyor. It may include sensors to detect the position of materials, detect jams, and ensure the conveyor runs smoothly. Automated control systems increase operational efficiency by reducing human intervention and improving overall system responsiveness.
Importance: A well-implemented control system improves accuracy, reduces operational errors, and increases the overall throughput of materials. It allows the conveyor system to respond dynamically to changes in production speed and load.
Maintenance Tip: Regularly check and calibrate sensors, update control system software, and perform diagnostic tests to ensure that the control system is functioning optimally.
How Conveyor System Parts Improve Efficiency and Productivity
In any industrial setting, efficiency and productivity are key to maintaining competitive advantage and optimizing operational costs. Conveyor systems are central to achieving both, as they provide a reliable, streamlined way to move materials across production lines, warehouses, and distribution centers. Understanding how conveyor system parts contribute to improving efficiency and productivity is essential for businesses looking to maximize their systems’ potential.
Optimizing Conveyor Speed with the Right Parts
One of the primary ways conveyor system parts improve productivity is by enabling optimal conveyor speeds. The speed at which materials are moved can directly impact the overall throughput and efficiency of a facility.
Function: The motor and drive unit regulate the speed of the conveyor belt, ensuring that materials are transported at a pace that aligns with the overall production schedule. Conveyor speed is often adjusted to match the flow of materials with different stages of production or packaging.
Impact on Efficiency: By fine-tuning the speed of the conveyor, businesses can ensure that materials are delivered at just the right time, reducing bottlenecks or unnecessary pauses in production. Faster conveyors may be beneficial for high-volume industries, while slower speeds might be preferred in environments that require more delicate handling.
Reducing Downtime Through Proper Maintenance of Conveyor System Parts
Another critical aspect of improving efficiency and productivity is reducing downtime, which can significantly disrupt production schedules. Proper maintenance of conveyor system parts plays a vital role in preventing unexpected breakdowns that can cause production delays.
Function: Routine maintenance ensures that all parts, including motors, rollers, idlers, and tensioners, are in good working condition. By regularly inspecting components for wear and tear, businesses can address issues before they become severe, reducing the likelihood of system failures.
Impact on Productivity: Downtime, even if brief, can have a ripple effect on overall productivity. When conveyor systems fail unexpectedly, workers may be idle, materials may pile up, and production schedules can be delayed. Effective maintenance prevents such issues, keeping production lines running smoothly and preventing costly stoppages.
Enhancing Automation with Advanced Conveyor System Parts
Modern conveyor systems often include sophisticated control systems that automate various processes, further boosting efficiency and reducing reliance on manual labor. These advanced systems incorporate sensors, programmable logic controllers (PLCs), and other automation tools.
Function: Control systems regulate the movement of materials through the conveyor system. They allow for real-time adjustments, such as speeding up or slowing down the conveyor based on demand, and they can even help detect jams or misalignments that would otherwise slow down operations.
Impact on Efficiency: Automated systems not only reduce the need for manual intervention but also improve the precision and speed of material handling. By automating material transport, companies can significantly cut down on human errors, improve safety, and streamline production processes.
Reducing Energy Consumption with Efficient Conveyor Parts
Energy consumption is a significant cost for many businesses, especially in high-volume environments where equipment runs continuously. Efficient conveyor system parts can help minimize energy use, contributing to both cost savings and a more environmentally friendly operation.
Function: Efficient motors and drive units are key to reducing energy consumption. Selecting energy-efficient components and optimizing system settings can ensure that the conveyor system operates at its peak without wasting power.
Impact on Productivity: By using energy-efficient parts, businesses can not only lower operating costs but also reduce the risk of system overheating or overuse, which can contribute to maintenance issues. A more energy-efficient system runs longer and more smoothly, leading to fewer repairs and interruptions.
Customizing Conveyor System Parts for Specific Applications
Different industries have specific requirements for material handling, and customizing conveyor system parts to meet those needs can significantly improve operational efficiency.
Function: Businesses can choose specialized conveyor belts, rollers, and drives that are designed for the unique demands of their industry. For example, a food processing plant may require wash-down conveyors that are easy to clean, while a warehouse may need slat conveyors for heavier loads.
Impact on Productivity: Customizing the conveyor system ensures that it is optimized for the exact type of material being transported, reducing inefficiencies caused by misalignment or improper handling. This customization also minimizes the risk of material damage, contributing to higher-quality outputs and reduced waste.
Selecting the Right Conveyor System Parts for Your Needs
Choosing the right conveyor system parts is crucial for optimizing the efficiency and longevity of your material handling system. With a wide range of components available, it’s important to select parts that are tailored to your specific operational needs, whether you’re moving light packages in a warehouse or handling heavy industrial materials. The right selection can reduce maintenance costs, improve system performance, and help avoid unnecessary downtime. Here’s a guide on how to select the best conveyor system parts for your needs.
Factors to Consider When Choosing Conveyor System Parts
When selecting conveyor system parts, it’s important to consider several factors that influence both the functionality and performance of the entire system. These factors help you align the right components with the demands of your specific environment and application.
Material Type: The type of materials being handled is a primary consideration when selecting conveyor parts. For example, lightweight items like small packages require different components compared to heavier, bulk materials like pallets or metal parts. Conveyor belts designed for light materials typically have different properties than those designed for heavy-duty use.
Environment: The working environment will also play a significant role in the selection process. For instance, food processing plants require wash-down conveyors that can withstand frequent cleaning and exposure to moisture, while a high-temperature factory may need heat-resistant conveyor belts to handle hot materials.
Speed and Load Capacity: Consider the required conveyor speed and load capacity for your operation. High-speed conveyors are typically used in environments where fast-moving products need to be handled, while slower, more robust conveyors are necessary for heavier loads or more sensitive materials that require careful handling.
Matching Conveyor System Parts to Your Specific Industry
Each industry has its own unique needs when it comes to conveyor systems, and selecting the right components ensures that the system operates smoothly and efficiently in your specific setting. Below are a few examples of how to match conveyor system parts to industry-specific requirements:
Manufacturing: In manufacturing environments, conveyors need to handle not only high volumes of materials but also often have to integrate with automated production lines. Rollers and idlers need to be robust, and motors should be capable of running continuously without failure. Choosing the right control systems can also optimize the integration of the conveyor into the production workflow.
Warehousing and Distribution: In warehouse and distribution centers, conveyors often need to move a variety of package sizes and weights. It’s essential to use modular conveyor belts that can be easily adjusted or replaced based on changing needs. Consider using gravity conveyors for lightweight items and powered conveyors for heavier loads that require consistent movement.
Food and Beverage: The food and beverage industry has stringent hygiene standards. Here, stainless steel conveyor parts that are easy to clean and corrosion-resistant are often required. Washdown conveyors, equipped with easy-to-clean surfaces, will help prevent contamination and ensure compliance with safety standards.
The Impact of Conveyor System Parts on Energy Efficiency
When selecting conveyor system parts, energy efficiency should also be a priority, especially for businesses looking to reduce operational costs and environmental impact. Components like motors, drive units, and rollers can all play a role in minimizing energy consumption while maximizing performance.
Motor Selection: Choosing energy-efficient motors is a key consideration when designing a conveyor system. Variable Frequency Drives (VFD) allow for adjustable speed control, ensuring that the motor operates only as needed and consumes the least amount of energy.
Drive Units and Rollers: Selecting energy-efficient drive units that reduce friction and wear will not only improve the system’s longevity but will also ensure that energy is not wasted. Low-friction rollers can make a big difference in reducing the amount of energy required to move materials along the conveyor.
Belt Materials: The type of material your conveyor belt is made from can also influence energy consumption. For example, using belts designed for low friction can reduce the motor’s load, thus improving energy efficiency and performance.
Durability and Maintenance Requirements of Conveyor System Parts
Durability is a key consideration when selecting conveyor system parts—especially in high-demand environments where the system runs continuously. Choosing durable components that require less maintenance will result in a more reliable system with lower operating costs.
Belt and Roller Durability: Conveyor belts made from materials such as urethane or steel mesh are more durable and suitable for rough or abrasive materials, while belts made from synthetic fibers might be better for lighter, non-abrasive materials. Similarly, high-quality rollers that are made from durable materials such as stainless steel or heavy-duty plastic will last longer, reducing the frequency of replacements.
Long-Term Maintenance: Select conveyor system parts that offer easy access for repairs and maintenance. For example, belts with easily replaceable sections and rollers with quick-release mechanisms make it easier for maintenance teams to perform repairs or replacements without causing excessive downtime.
Cost-Effectiveness: While opting for the most durable components may initially seem like a higher upfront cost, the long-term savings in reduced maintenance, repairs, and replacements can justify the investment. Choosing high-quality parts is an investment in the efficiency and longevity of the system.
Working with Experts to Customize Your Conveyor System Parts
In many cases, working with conveyor system experts or engineers can help you select the most appropriate parts for your specific needs. They can assist in customizing the conveyor system to meet your unique operational requirements, ensuring that the system operates at peak efficiency from the start.
Consultation: If you’re unsure about the best configuration of parts, consider consulting with a conveyor system provider. They can guide you through the process of choosing components based on your specific needs, helping to design a system that is both efficient and cost-effective.
Tailored Solutions: For industries with specialized needs, such as the food industry or chemical handling, conveyor parts may need to be customized. Conveyor system experts can provide tailored solutions, such as belts with specific coatings or rollers designed to handle specific environmental conditions.
Maintenance and Care of Conveyor System Parts for Longevity
Proper maintenance and care are essential for ensuring that your conveyor system parts continue to perform at their best over time. Just like any other piece of machinery, conveyor systems are subject to wear and tear, which can lead to breakdowns or reduced efficiency if not regularly maintained. By performing routine maintenance on the key components of your conveyor system, you can extend the lifespan of the equipment, reduce the risk of unexpected failures, and ultimately enhance productivity. Here’s a guide to the maintenance and care of conveyor system parts to ensure longevity.
Routine Inspections: The First Step in Preventative Maintenance
Regular inspections are one of the most effective ways to identify potential issues before they become significant problems. Routine checks help ensure that each conveyor system part is functioning as it should, and can help detect wear or damage early on.
Function: Inspections should cover all critical parts, including conveyor belts, motors, rollers, idlers, and drive units. Look for signs of wear, misalignment, or damage that could affect performance, such as cracks in belts, damaged rollers, or loose components.
Importance: By catching problems early, businesses can prevent costly repairs, avoid system downtime, and ensure that the conveyor operates at peak efficiency.
Proper Lubrication: Ensuring Smooth Operation
Proper lubrication is crucial for keeping many of the moving parts of a conveyor system, such as rollers, motors, and drive units, running smoothly. Lubricating these parts reduces friction, minimizes wear and tear, and helps prevent overheating.
Function: Lubrication minimizes the friction between moving parts, which prevents components like rollers and gears from grinding against each other and wearing out prematurely. It also reduces the load on the motor, ensuring that the conveyor system runs efficiently.
Importance: Without proper lubrication, parts will wear faster, and the system will become less efficient, which can lead to unnecessary energy consumption and higher operational costs. Additionally, lack of lubrication can result in overheating, which can damage the system permanently.
Conveyor Belt Maintenance: Extending Belt Lifespan
Peralatan conveyor belt is one of the most critical parts of a conveyor system, and its maintenance is essential for ensuring the entire system operates efficiently. Over time, belts can experience wear, stretching, or damage, which can impact their ability to transport materials.
Function: Regular maintenance of the conveyor belt includes checking for signs of damage, cleaning the belt to prevent material buildup, and ensuring that it is correctly aligned.
Importance: A damaged or poorly maintained belt can lead to disruptions in the production process, increased energy consumption, and more frequent repairs or replacements. Properly maintaining the belt ensures smooth operation, improves efficiency, and reduces overall maintenance costs.
Monitoring and Adjusting Tension: Preventing Overstretching
Conveyor belts must maintain the right level of tension to function properly. If the belt is too loose, it may slip or cause misalignment, while a belt that is too tight can cause excessive wear on the motor and drive units.
Function: Tensioners are used to adjust the tension of the conveyor belt, ensuring that it remains at an optimal level for efficient operation. Adjusting the tension helps maintain smooth movement, prevents sagging, and ensures that the belt doesn’t slip or become misaligned.
Importance: Proper tensioning of the conveyor belt prevents premature damage to the belt and motor, helps prevent slippage, and reduces unnecessary wear on system components.
Cleaning and Preventing Debris Build-up
The accumulation of dust, dirt, or materials on the conveyor system parts can lead to inefficiencies and even damage over time. Regular cleaning is a critical part of maintaining your conveyor system.
Function: Cleaning prevents debris from building up on components like the conveyor belt, rollers, motors, and idlers, which can lead to system failure or reduced efficiency. For example, dust or debris on rollers can create excessive friction, causing parts to wear out faster.
Importance: A clean conveyor system operates more efficiently and lasts longer. It also reduces the risk of contamination, particularly in industries like food production, where hygiene is critical.
Replacing Worn or Damaged Parts on Time
Even with proper care and maintenance, conveyor system parts will eventually experience wear and tear, especially in high-demand environments. It’s essential to replace worn or damaged parts promptly to prevent further damage to other components and to keep the system running smoothly.
Function: Parts such as rollers, motors, and conveyor belts are subject to wear over time. When a part shows signs of damage or reduced performance, it should be replaced to avoid more serious problems that can result in costly repairs or downtime.
Importance: Timely replacement of damaged or worn-out parts ensures that the conveyor system continues to operate at its best, preventing breakdowns and extending the system’s lifespan.
Staff Training: Ensuring Proper Operation and Maintenance
Proper operation and maintenance require a well-trained staff who understands how to care for and manage the conveyor system parts. Educating employees on how to handle the system, perform routine inspections, and identify potential issues is essential for maintaining the system’s efficiency and longevity.
Function: Staff should be trained on proper procedures for operating and maintaining the conveyor system. This includes understanding how to adjust tension, lubricate components, and handle parts safely.
Importance: Well-trained staff are more likely to spot early signs of wear or damage and prevent mishaps. Proper training ensures that the system is used correctly, reducing the risk of damage and improving overall productivity.